In this article:
- Introduction
- The Manufacturing Knowledge Crisis
- Digital Knowledge Preservation: A Strategic Imperative
- The Four Components of Effective Knowledge Preservation
- Implementation Strategy: Building Your Knowledge Preservation System
- Measuring ROI: The Business Case for Knowledge Preservation
- Beyond Continuity: Strategic Benefits of Digital Knowledge Preservation
- The AI-Enhanced Knowledge Future
- Conclusion: Knowledge as Strategic Asset
In manufacturing facilities across the globe, critical operational expertise is walking out the door. The wave of retirements among experienced personnel, combined with increasing equipment complexity and historically high turnover rates, has created a knowledge crisis that threatens operational continuity.
💡
This article explores how forward-thinking manufacturers are systematically preserving institutional knowledge—transforming tacit expertise into accessible digital assets that accelerate training, improve troubleshooting, and build operational resilience.
The Manufacturing Knowledge Crisis
The Demographic Challenge
The manufacturing workforce is undergoing unprecedented transition:
- 2.6 million baby boomers will retire from manufacturing by 2025 (Deloitte)
- Average manufacturing worker age: 44.5 years, compared to 42.3 across all industries
- 27% of manufacturing workforce eligible for retirement within 5 years
- 89% of manufacturers report moderate to severe talent shortages
The Knowledge Complexity Problem
Today's manufacturing environment demands more expertise than ever:
- 78% increase in equipment technological complexity over past decade
- Average manufacturing facility utilizes 12+ disparate systems requiring specialized knowledge
- 87% of critical manufacturing processes rely on tacit knowledge not formally documented
- 73% of manufacturers report "significant concern" about loss of specialized expertise
The Training and Retention Challenge
Passing knowledge to new workers faces fundamental obstacles:
- Average time to proficiency for manufacturing technicians: 12-18 months
- New hire turnover within first year: 27% and rising
- Training effectiveness ratings by operations managers: just 5.7/10
- Knowledge transfer success rates for departing experts: below 40%
⚠️
Digital Knowledge Preservation: A Strategic Imperative
Case Study: Specialty Chemicals Manufacturer
A leading specialty chemicals manufacturer implemented a comprehensive digital knowledge capture program after calculating that 43% of their critical operational expertise would be eligible for retirement within 3 years.
Before Implementation
- Critical knowledge formally documented: 31%
- New operator time to proficiency: 14.2 months
- Production deviations attributed to knowledge gaps: 27%
- Troubleshooting success rate for new technicians: 52%
- Training effectiveness rating: 6.1/10
After Implementation
- Critical knowledge formally documented: 87% (181% improvement)
- New operator time to proficiency: 5.3 months (63% reduction)
- Production deviations attributed to knowledge gaps: 8% (70% reduction)
- Troubleshooting success rate for new technicians: 84% (62% improvement)
- Training effectiveness rating: 8.7/10 (43% improvement)
🗣️
The Four Components of Effective Knowledge Preservation
1. Visual Process Documentation
Moving beyond traditional written procedures:
- Recorded demonstrations of critical procedures with expert narration
- Multi-angle video capture of complex manual operations
- Screenshots with annotations highlighting key components and caution points
- Transcripts of support sessions with auto tag and problem classification
2. Interactive Troubleshooting Guides
Converting expert diagnostic approaches into guided pathways:
- Decision-tree troubleshooting flows based on expert approaches
- Visual indicators of normal vs. abnormal conditions
- Captured expert sessions addressing common issues
- Equipment-specific diagnostic procedures with tribal knowledge incorporated
3. Contextual Knowledge Organization
Making information findable when and where needed:
- Equipment-specific knowledge libraries
- Intelligent search engine to find the correct guided path for the task
- Easy access by mobile phone, tablet or computer
4. Knowledge Validation and Refinement
Ensuring accuracy and continuous improvement:
- Expert review processes for captured knowledge
- Usage analytics to identify gaps and improvement areas
- Feedback mechanisms for continuous refinement
Implementation Strategy: Building Your Knowledge Preservation System
Phase 1: Critical Knowledge Assessment
Weeks 1-4
- Identify highest-risk expertise areas based on retirement eligibility
- Document critical processes currently dependent on tribal knowledge
- Prioritize knowledge capture based on operational impact
- Establish baseline metrics for knowledge availability and effectiveness
Phase 2: Capture Methodology Development
Weeks 5-8
- Define software for knowledge preservation capture
- Upload current documented knowledge on the knowledge base - auto convert to standard templates
- Define and train users for initial implementation
Phase 3: Priority Knowledge Capture
Weeks 9-16
- Begin structured capture of highest-priority expertise
- Implement digital repository with appropriate organization
- Create mechanisms for field access to captured knowledge
- Establish integration with training and onboarding programs
Phase 4: Continuous Knowledge Ecosystem
Months 5-12
- Implement ongoing capture processes for routine operations
- Deploy remote expert session recording capabilities
- Develop knowledge analytics and gap identification
- Create recognition programs for knowledge contribution
⚠️
Measuring ROI: The Business Case for Knowledge Preservation
Operational Continuity Value
Calculate the impact of preserved operational knowledge:
- Reduced production disruptions due to knowledge gaps
- Faster resolution of abnormal conditions
- Higher first-time quality through consistent procedures
- Reduced variability in process outcomes
Training Efficiency Gains
Quantify the improvements in workforce development:
- Faster time to proficiency for new personnel
- Reduced shadow training requirements
- Higher knowledge retention from training
- Improved employee satisfaction and retention
Risk Mitigation Impact
Measure the value of reduced operational risk:
- Lower compliance deviations through consistent procedures
- Reduced safety incidents through captured best practices
- Decreased equipment damage from improper procedures
- Enhanced business continuity planning
💰
Beyond Continuity: Strategic Benefits of Digital Knowledge Preservation
1. Operational Excellence Foundation
Building the basis for continuous improvement:
- 73% of manufacturers report improved standard work adherence
- 68% achieve better cross-shift consistency
- 81% reduce process variability in key operations
- 76% accelerate continuous improvement initiative implementation
2. Enhanced Organizational Agility
Responding faster to changing conditions:
- 64% faster deployment of new procedures across facilities
- 71% more effective cross-training for operational flexibility
- 58% improved response to supply chain disruptions
- 84% faster troubleshooting of novel operational issues
3. Talent Attraction and Retention
Creating a more supportive work environment:
- 67% of manufacturing employees prefer employers with strong knowledge systems
- 73% report higher job satisfaction when proper support is available
- 58% reduction in early-career turnover with effective knowledge support
- 82% improvement in employee confidence and empowerment
The AI-Enhanced Knowledge Future
Forward-thinking manufacturers are preparing for the next evolution in knowledge management:
Knowledge Mining and Pattern Recognition
Extracting insights from operational history:
- AI analysis of successful vs. unsuccessful troubleshooting approaches
- Pattern recognition in process deviations and resolutions
- Automatic identification of best practices from operational data
- Correlation of expert behaviors with optimal outcomes
Contextual Knowledge Delivery
Providing exactly what's needed, when needed:
- Real-time guidance based on current operational conditions
- Predictive support for emerging issues based on pattern recognition
- Personalized knowledge delivery based on experience level
- Just-in-time training for infrequently performed procedures
🔮
Conclusion: Knowledge as Strategic Asset
The transition from person-dependent expertise to systematically captured institutional knowledge represents perhaps the most significant operational transformation available to manufacturers today. As workforce demographics continue to shift and equipment complexity increases, the ability to preserve and transfer critical knowledge will become not just advantageous but essential for operational continuity.
Manufacturers who implement comprehensive knowledge preservation systems today aren't just addressing an immediate demographic challenge—they're building a foundation for operational excellence that will provide competitive advantage for decades to come.
Key Takeaways
- The manufacturing sector faces an unprecedented loss of expertise with 2.6 million baby boomers retiring by 2025
- Digital knowledge preservation systems reduce new technician time-to-proficiency by 64% and improve knowledge retention by 78%
- Effective knowledge preservation requires visual documentation, interactive troubleshooting guides, contextual organization, and continuous validation
- Implementation follows a four-phase approach spanning 5-12 months, focusing equally on technology and human processes
- Benefits extend beyond operational continuity to include improved quality, organizational agility, and employee retention
Knowledge Preservation
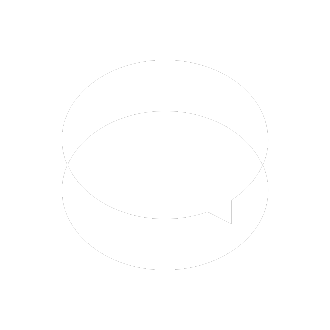