In this article:
- Introduction
- The Global Manufacturing Collaboration Challenge
- Case Study: Multinational Automotive Components Manufacturer
- Five Critical Areas Transformed by Visual Collaboration
- Implementation Strategy: Building Your Multi-Site Collaboration Ecosystem
- Measuring Multi-Site Manufacturing Excellence
- The Future of Connected Manufacturing Operations
- Conclusion: From Distributed Sites to Unified Operations
In today's global manufacturing landscape, geographical distribution has become both a strategic advantage and an operational challenge. Leading manufacturers operate an average of 7-12 production facilities across multiple countries, creating complex coordination challenges that impact quality, efficiency, and innovation.
💡
This article explores how forward-thinking manufacturers are breaking down geographical barriers through visual collaboration technology—transforming disconnected facilities into synchronized teams that share knowledge instantaneously, solve problems collaboratively, and implement best practices consistently across global operations.
The Global Manufacturing Collaboration Challenge
The Geographic Expertise Disparity
Manufacturing excellence is unevenly distributed across operations:
- 73% of manufacturers report significant performance variations between facilities producing identical products
- Specialized expertise is typically concentrated in primary/headquarters locations
- Remote or newer facilities experience 2.7× higher quality deviation rates
- Technical issue resolution takes 3-5× longer at satellite locations
Cross-Facility Knowledge Barriers
Traditional knowledge sharing methods are failing in modern operations:
- 67% of critical process improvements remain "trapped" at originating facilities
- Average time to transmit best practices between facilities: 4.7 months
- Only 23% of cross-facility knowledge exchanges are deemed "highly effective"
- 82% of process improvements are never fully implemented in secondary locations
The Costly Travel Reality
Physical travel creates significant inefficiencies:
- Average multinational manufacturer spends $160K annually per site on cross-facility expert travel easily reaching the million-dollar figure when having more than 8 locations
- Technical experts spend 24-37% of working time in transit between facilities
- Production issues experience 72-hour average delay awaiting on-site expert assistance
- Typical new facility ramp-up requires 450+ person-days of headquarters staff travel
⚠️
Case Study: Multinational Automotive Components Manufacturer
A leading automotive components manufacturer with 14 production facilities across North America, Europe, and Asia implemented a comprehensive visual collaboration program to address growing disparities in quality and efficiency between facilities.
Before Implementation
- Cross-facility problem resolution time: 8.4 days average
- Process standardization compliance: 63% across facilities
- Technical expert travel: 43% of available working time
- Quality performance gap between best/worst facilities: 37%
- Best practice implementation time: 5.3 months average
- New product launch synchronization: 68% consistency
After Implementation
- Cross-facility problem resolution time: 1.7 days average (80% reduction)
- Process standardization compliance: 92% across facilities (46% improvement)
- Technical expert travel: 12% of available working time (72% reduction)
- Quality performance gap between best/worst facilities: 11% (70% reduction)
- Best practice implementation time: 1.2 months average (77% reduction)
- New product launch synchronization: 94% consistency (38% improvement)
🗣️
Five Critical Areas Transformed by Visual Collaboration
1. Cross-Facility Troubleshooting
Bringing specialized expertise to any location instantly:
- 71% reduction in time to engage appropriate expertise for complex issues
- Real-time visual diagnostics with immediate feedback loops
- 67% higher first-time resolution rates for technical issues
- Multi-facility collaboration for novel or challenging problems
2. Process Standardization
Ensuring consistent implementation of best practices:
- Visual verification of process execution across all facilities
- Real-time guidance during procedure implementation
- 82% improvement in adherence to standard work
- Interactive training with visual confirmation of understanding
3. New Product Introduction
Accelerating synchronized global launches:
- 63% faster knowledge transfer during production ramp-up
- Visual demonstration of critical processes from lead facility
- Remote expert guidance during initial production runs
- Live problem-solving during launch phase
4. Equipment Installation and Qualification
Ensuring consistent deployment across facilities:
- Remote OEM expert support during installation
- 57% reduction in equipment qualification time
- Visual verification of proper setup and calibration
- Standardized commissioning procedures with visual guidance
5. Continuous Improvement Knowledge Transfer
Spreading innovation across the manufacturing network:
- 73% increase in cross-facility improvement idea implementation
- Visual demonstration of improvement concepts
- Real-time feedback during implementation attempts
- Creation of visual knowledge base for future reference
💰
Implementation Strategy: Building Your Multi-Site Collaboration Ecosystem
Phase 1: Foundational Assessment
Weeks 1-4
- Map existing cross-facility communication flows and gaps
- Identify highest-impact use cases based on business value
- Assess technical infrastructure at all locations
- Establish baseline metrics for key performance indicators
Phase 2: Focused Pilot Implementation
Weeks 5-12
- Deploy visual collaboration tools for priority use cases
- Develop standardized protocols for different collaboration types
- Create documentation templates and knowledge capture workflows
- Train pilot participants at all participating facilities
Phase 3: Process Integration
Weeks 13-24
- Integrate visual collaboration into standard work procedures
- Implement knowledge management system for session recordings
- Create role-specific training and certification programs
- Develop metrics and reporting for collaboration effectiveness
Phase 4: Enterprise Optimization
Months 6-12
- Scale implementation across all facilities and use cases
- Create centers of excellence for specialist knowledge sharing
- Implement continuous improvement feedback loops
- Develop advanced collaboration capabilities with mixed reality
⚠️
Measuring Multi-Site Manufacturing Excellence
Operational Consistency Metrics
Track the synchronization of your manufacturing network:
- Process standardization compliance across facilities
- Performance variation between best and worst facilities
- First-time quality consistency for identical products
- Adherence to standard work procedures
Knowledge Transfer Effectiveness
Measure how effectively expertise flows between facilities:
- Time to implement process improvements across all locations
- Successful adaptation rate of innovations from other facilities
- Cross-facility problem resolution time
- Reduction in duplicate problem-solving efforts
Resource Optimization
Quantify improvements in resource allocation:
- Reduction in travel time and costs for technical specialists
- Expert utilization across multiple facilities
- Specialist productivity improvement
- Cross-facility support capacity
Financial Impact Measurement
Calculate the comprehensive business impact:
- Cost reduction through standardized best practices
- Downtime reduction across facilities
- New product launch acceleration
- Quality cost improvements from consistent execution
The Future of Connected Manufacturing Operations
Immersive Collaboration Environments
The next generation of cross-facility interaction:
- Mixed reality overlays for equipment interaction
- Digital twin integration with live collaboration
- Spatial computing for complex process visualization
- Interactive 3D modeling for cross-facility problem-solving
AI-Enhanced Cross-Facility Learning
Machine learning will transform knowledge transfer:
- Automatic identification of best practices from performance data
- Predictive guidance based on cross-facility patterns
- Intelligent routing of issues to appropriate expertise
- Automated translation for global collaboration
Continuous Knowledge Networks
Beyond episodic collaboration to constant connection:
- Always-on virtual presence between sister facilities
- Real-time performance visualization across the network
- Continuous improvement communities spanning all locations
- Global centers of excellence with virtual deployment capabilities
🔮
Conclusion: From Distributed Sites to Unified Operations
The transformation from geographically isolated facilities to a synchronized manufacturing network represents one of the most significant operational evolutions available to modern manufacturers. As operations become increasingly distributed, the ability to collaborate visually across locations becomes not just advantageous but essential for competitive performance.
Visual collaboration technology is eliminating the traditional penalties of distance—enabling expertise to flow instantly to where it's needed, ensuring consistent execution of best practices, and creating truly global teams that transcend physical limitations.
The manufacturers embracing this transformation aren't just improving efficiency—they're building resilient, adaptive operations that can maintain excellence regardless of where production occurs, setting new standards for what's possible in global manufacturing.
Key Takeaways
- Leading manufacturers are achieving 37% faster problem resolution and 52% better cross-facility standardization through visual collaboration tools
- The performance gap between top and bottom-performing facilities within the same company often exceeds 40% without effective collaboration systems
- Five critical areas transformed by visual collaboration include cross-facility troubleshooting, process standardization, new product introduction, equipment installation, and continuous improvement
- Successful implementation follows a four-phase approach focusing equally on technology, process redesign, and cultural development
- The future of manufacturing operations will feature immersive collaboration environments, AI-enhanced learning, and continuous knowledge networks
Multi-Site Collaboration
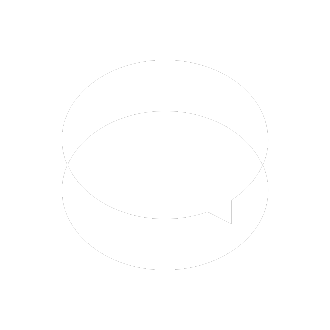