In this article:
Introduction
In today's industrial manufacturing landscape, every minute of downtime translates to thousands in lost revenue. For a mid-sized manufacturing operation, unplanned downtime costs an average of $260,000 per hour according to Aberdeen Research.
💡
As manufacturers face growing complexity in equipment and processes, combined with the accelerating retirement of experienced personnel, solving technical problems efficiently has never been more challenging—or more crucial to operational success.
This article explores how remote visual assistance technology is transforming troubleshooting processes and how leading manufacturers are achieving measurable downtime reductions while preserving institutional knowledge for the future.
The Triple Challenge Facing Industrial Manufacturers
1. The Knowledge Exodus Crisis
The manufacturing sector is experiencing an unprecedented loss of expertise:
- 2.6 million baby boomers will retire from manufacturing by 2025 (Deloitte)
- 89% of manufacturers report moderate to severe shortages of qualified technicians
- Average time to proficiency for new technical hires: 12-18 months
⚠️
2. Multi-Site Complexity
Today's manufacturing operations face unprecedented geographical distribution:
- Average large manufacturer manages 9+ production facilities
- 67% operate facilities across multiple countries
- Cross-facility knowledge sharing rated as "highly ineffective" by 72% of maintenance managers
3. Rising Equipment Complexity
Modern industrial equipment requires deeper technical expertise:
- 78% increase in embedded sensors over the past 5 years
- 340% increase in data points generated per machine
- 65% of maintenance personnel report feeling "overwhelmed" by technical complexity
The Transformative Impact of Remote Visual Assistance
Case Study: Global Automotive Parts Manufacturer
A leading automotive parts manufacturer with 14 global facilities implemented remote visual assistance after calculating annual downtime costs of $4.7 million.
Metric | Before | After | Improvement |
---|---|---|---|
Downtime per incident | 4.2 hours | 1.8 hours | 57% reduction |
Expert travel required | 63% of cases | 12% of cases | 81% reduction |
First-time fix rate | 52% | 87% | 67% improvement |
Knowledge transfer success | 41% | 92% | 124% improvement |
🗣️
How Remote Visual Assistance Actually Works
Unlike standard video calls, modern remote visual assistance platforms like AssistLink provide specialized capabilities designed for industrial environments:
1. One-way video streaming
- Functions in low bandwidth and poor lighting conditions
- Provides higher quality than standard video calling
- Focuses all attention on the equipment, not faces
2. Interactive guidance tools
- Real-time annotation directly on live video
- Freeze-frame capabilities for detailed instruction
- Pointer tools for precise component identification
3. Knowledge capture
- Session recording with searchable transcripts
- Digital reporting for audits and compliance
- Integration with existing systems and processes
The Dollars and Cents: Calculating Your Potential Savings
Step 1: Calculate Current Downtime Costs
- Average downtime incidents per month: [Your number]
- Average hours per incident: [Your number]
- Cost per hour of downtime: [Your number]
- Monthly downtime cost = Incidents × Hours × Cost per hour
Step 2: Factor in Travel and Labor Costs
- Expert travel instances per month: [Your number]
- Average travel cost per instance: [Your number]
- Travel hours per month × Expert hourly cost
- Total travel cost = Direct travel costs + Expert time cost
Step 3: Project Conservative Improvements
- Downtime reduction: 35% (conservative industry average)
- Travel reduction: 75% (conservative industry average)
- First-time fix improvement: 40% (conservative industry average)
Step 4: Calculate ROI Timeframe
- Implementation and training costs
- Monthly savings from reduced downtime and travel
- Payback period = Implementation costs ÷ Monthly savings
💰
Implementation Roadmap: From Decision to Deployment
Decision Phase
Immediate Technical Requirements
- Calculate current downtime costs
- Assess connectivity limitations
- Evaluate the need of better troubleshooting-focused communication tools
- Determine security requirements
Complete Solution Evaluation
- Assess communication tools like AssistChat, AssistView and WiseSpace
- Evaluate digital documentation options (E-Reports)
- Consider knowledge capture capabilities (AssistLink platform)
- Verify system integration possibilities
Future-Proof Technology
- Verify AI and analytics capabilities
- Ensure multi-site scalability
- Assess knowledge preservation tools
- Confirm vendor innovation roadmap
Days 1-30: Pilot & Training
- Deploy to selected pilot team
- Train users on core functionality
- Document common use cases
- Create standard workflows
- Establish success metrics
- Collect initial feedback
- Test connectivity across locations
- Create user adoption materials
Days 31-60: Expansion & Integration
- Scale to additional teams
- Connect with existing systems
- Develop knowledge capture workflow
- Begin measuring ROI results
- Refine training and onboarding
- Create ongoing support structure
- Document success stories
- Share best practices across sites
💡
Beyond Downtime: Additional Benefits for Manufacturers
1. Preservation of Critical Knowledge
Remote visual assistance creates a searchable visual repository of maintenance and troubleshooting procedures, ensuring critical knowledge doesn't leave with retiring experts:
- 87% of manufacturers report improved knowledge retention
- 76% reduction in time to proficiency for new technicians
- 93% faster access to expert knowledge for complex issues
2. Enhanced Multi-Site Collaboration
Breaking down geographical barriers delivers unexpected operational improvements:
- 68% increase in cross-facility standardization of best practices
- 47% reduction in repeated equipment failures
- 82% improvement in global team collaboration scores
3. Streamlined Audits and Compliance
Visual documentation transforms audit processes:
- 54% reduction in audit preparation time
- 72% decrease in non-conformance issues
- 89% faster resolution of compliance-related questions
Conclusion: The Future of Industrial Troubleshooting is Visual
The data is clear: remote visual assistance technology represents a transformative advancement in industrial support, with measurable impacts on downtime reduction, knowledge preservation, and operational resilience.
As manufacturers face increasing equipment complexity and accelerating knowledge loss, visual communication platforms will become not just advantageous but essential for maintaining competitive operations.
🔮
Manufacturers who implement these solutions today are not just solving immediate support challenges—they're building the foundation for more resilient operations in an increasingly complex industrial landscape.
Key Takeaways
- Remote visual assistance reduces equipment downtime by 42% on average
- First-time fix rates improve by 67% with visual guidance
- ROI is typically achieved within 3-6 months
- Knowledge preservation ensures critical expertise doesn't retire with your experts
- Multi-site operations see 68% improvement in standardization
Remote Visual Assistance
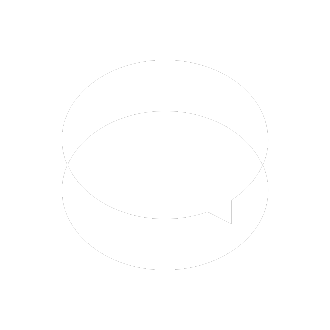